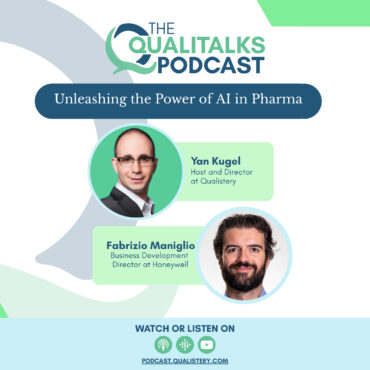
Unleashing the Power of AI in Pharma [Fabrizio Maniglio]
abrizio Manilio discusses the role of digitalization and AI in the life sciences industry. He shares insights into the future of technology, the importance of understanding capabilities, and the potential […]